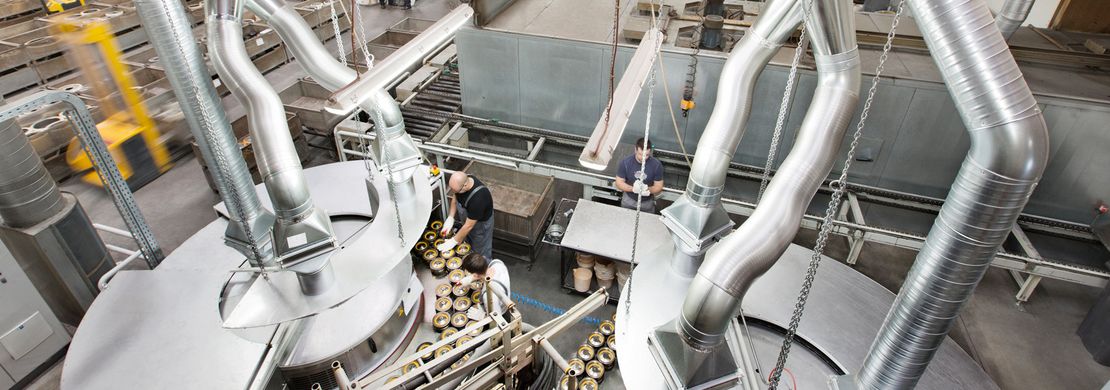
Casting and post-treatment
Our second plant became operational in 2002 and has been continually expanded ever since. On an area of 10,000 square metres, we produce up to 12,000 wheels and castors with VULKOLLAN® or polyurethane treads every day at this, the world’s most cutting-edge production facility. Electrically conductive VULKOLLAN®-ELF and TRACTOTHAN® wheels are also produced here in line with patented procedures.
After machining is carried out in our first plant, all metal cores are blasted here to achieve a pure metallic surface, and are then cleaned of residue in special washing machines, degreased and vacuum-dried. This is followed by a sensitive process step – the application of the bonding agent. The cores are sprayed with a special bonding agent in computer-controlled systems, thus ensuring the required bonding between wheel centre and covering.
Our wheel centres are in fact heated to a prescribed degree using special fusion ovens before the actual coating takes place in order to bring the core and casting material to the same temperature and to chemically activate the bonding agent. The prepared cores are then coated with a range of different wheel tread materials, such as VULKOLLAN® or PEVOPUR®, either by machine casting or hand casting.
In the manufacture of polyurethane wheel treads in hot casting, chemical reaction processes take place, under strictly controlled conditions, and do not terminate until long after the material has hardened. After-treatment of the coated wheels – a process known as curing – is therefore of great importance and is crucial to the excellent quality of our products. In our curing room, all products undergo a special procedure based on predefined parameters with regard to temperature, humidity and curing duration.